Wire threaded inserts
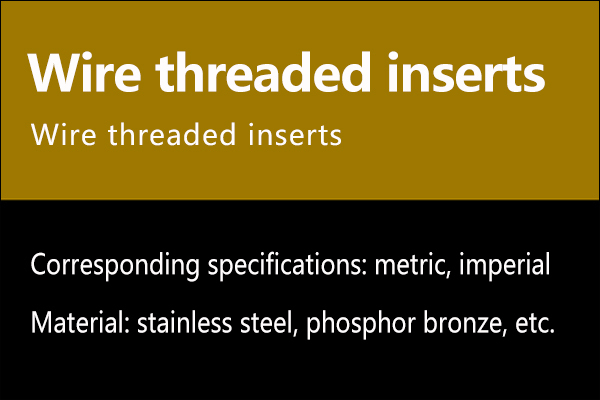
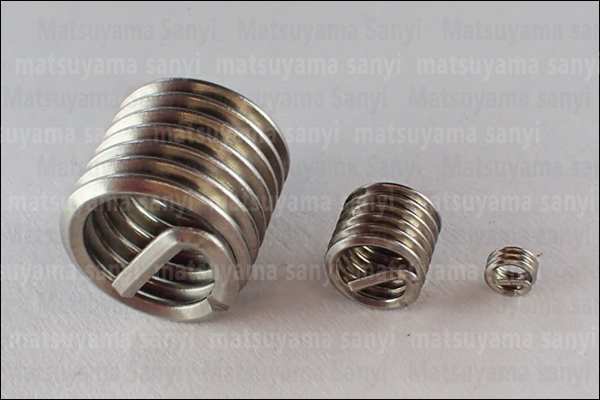
Clever use of springback for a more reliable threaded connection
By adjusting the thread pitch and angle error, the stress is evenly distributed, thereby strengthening the bond between the workpiece and the screw.
When winding symmetrical rhombus wire, the angle will change due to internal stress
Therefore, in traditional products, the contact between the base material and the screw is close to a line rather than a surface, and the stress distribution is uneven.
Therefore, a product with a wider contact surface is achieved by pre-calculating the winding variation and winding the wire at different angles
Currently M3 to M12 have been converted to surface contact wire thread inserts
The main uses of wire thread inserts
1. Increase the strength of internal threads
Light metal, cast iron, resin, etc. have weak internal threads and cannot obtain high fastening force. By inserting a wire thread into these workpieces
It can balance the stress on each thread and increase the tightening force, achieving a strong and reliable tightening effect.
2. Improve the durability of internal threads
Prevent internal threads from being damaged due to wear, corrosion, vibration, heat, etc., and prevent workpiece damage to achieve reliable screw tightening
3. Repair defective internal threads
Defective threaded holes or damaged threaded holes that occur during the manufacturing process can be repaired by using wire thread inserts
4. Reduce total cost
By using wire thread inserts, the diameter of the external thread and the length of the fitting can be reduced, and weight and volume can be reduced
This greatly contributes to reducing the total cost of products and improving quality